Reality: When it comes to root causes of physical and mental health issues, a person's work and home experiences are inseparable. Therefore, health and safety programs need to look at the whole person, not just what happens when that person shows up for work.
Rhonda: You have to pay attention to more than the work when interacting with employees. Often personal issues outside the workplace can have a significant impact on their performance and work relationships.
Jonathan: The holiday season is when people are most distracted, leading to one of the highest risks of injury. We've found that leaders initiating personal conversations with employees at this time of year is meaningful and works. Maybe an employee wants to share something job-related or perhaps wants to talk about what they'll be doing with their kids over the holidays.
Jen: When you're changing the culture around health and safety, it is important employees know they have resources and support for when they need it, which could be weeks, months or years down the road. We have a variety of programs in place to help manage these additional stressors for our mining employees who do shift work and are potentially away from their families.
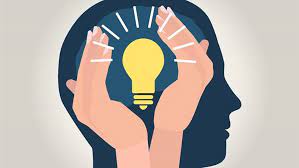
Based on our employee total well-being assessment completed in early 2021, 78% of participants agree that SMS Equipment is committed to ensuring employees’ psychological safety.